RECLAIM: An EU Rejuvenation Project to Save Old Manufacturing Equipment
- Constant Tedder
- Jul 21, 2023
- 5 min read
‘Repair cafés’ are on the rise as a way to repair old things instead of replacing them. This is not only sustainable but it also saves money. The same development is taking place in the manufacturing industry. Researchers of the EU project RECLAIM are developing algorithms and programmes to make predictions about the remaining service life of machines, to extend their life expectancy, and to modernise the plants. If it is possible to maximise the service life of manufacturing plants, both the environment and companies will benefit.
—
Until a few years ago, anyone who found their home appliances no longer working was faced with only one option: buying a replacement. However, for more than a decade, the repair café movement has helped people repair their old machines by working with expert volunteers. This saves people money and feeds into the idea of a circular economy in which raw materials can be reused repeatedly.
It is a concept that offers hope for Europe’s manufacturing industry, where many large production plants are approaching their natural end of life. Replacing the old equipment too early is an unnecessary expense while replacing it too late would result in production losses and chaos. Ecologically and economically, it would make the most sense to optimally use or even extend the service life of a machine.
You might also like: The EU’s Common Charging Solution to Manage the E-Waste Crisis
Old Machines With New Strengths
Solving this can be achieved through a combination of sensor technology, data sets and digital tools that provide an informed decision-making framework, explained Melanie Gralow from the Steinbeis Europa Zentrum, an organisation for innovation consulting and research funding based in Karlsruhe, Germany. To do this, she said, one analyses the current running times of a plant, what faults occur, and what risk components exist.
“Based on that, you can then make predictions and extend the time a machine is in operation.”
Algorithms and programmes to make predictions about the remaining life of machines to extend their life expectancy and to modernise plants are being developed by experts in the EU research programme RECLAIM, for example.
First, those involved in the project look at specific use cases. However, the solutions for this must be designed flexibly so they can be transferred to other industries and other production systems.
“The parameters used have a certain degree of flexibility, for example which parameters are used or from which parameters values are read in,” Gralow explained. In addition, new standards could emerge from projects like RECLAIM and facilitate broad applicability as industry standards.
Technical Solutions Already Exist
Fundamental questions need to be clarified, such as how sensor technology and data acquisition can be combined to monitor the machines in real-time, and how software and algorithms can then access and evaluate this data. Another question is what role can machine learning and “digital twins”, a complete software model of the physical plant, play. Only when these steps are clear can the optimisation of the respective plant begin.
Often, no new technical methods need to be developed.
“We see that the market is lagging behind what is possible,” said Jesus De La Quintana of Tecnalia, an applied research centre in the Basque Country, Spain. One task, he explained, is to inform potential customers about such solutions and to demonstrate the possibilities. Companies nowadays often do not even think about making an old plant fit for a second life instead of replacing it.
“We’re not talking about an evolution here but a revolution,” he said.
But technology is not everything. Often, employees with many years of experience know the tricks of the trade to keep an old production line running as smoothly as possible and with the best quality. When these experts leave a company, one machine or another can quickly become unusable.
“Sustainability and efficiency don’t just mean digitalisation. They also mean storing knowledge digitally,” De La Qintana emphasised.
Are Machines as a Service the Answer?
Taking this approach further, a new business model emerges – “Machines as a service” – where production facilities lease their machines to customers.
The Hamburg-based company Harms & Wende has gained some early experience with this. The company produces friction welding machines and, in the course of the RECLAIM project, has also started to lease its products, including maintenance. Maximising the service life of the equipment has thus become an integral part of the revenue model.
On the hardware side, Harms & Wende has redesigned the machines so that they can be used in a modular and scalable way. Online sensors monitor the system’s condition and give an early warning if potential problems are on the horizon. A special interface enables maintenance personnel to interact with the system conveniently, even via remote maintenance. The provider can even import software updates so that machines that have been in operation for a long time can also participate in technical developments.
The new business model has already found its first customer. If all developments go as hoped, Harms & Wende expects to halve operating costs and extend the life of the plant by eight years.
“Things often change very suddenly, and that can make it risky for a company to spend money on big equipment,” said De La Quintana, who sees great potential in this model.
Leased manufacturing machines would therefore make it easier to venture into a business field. It also increases the likelihood that rental companies will design their machines in such a way that they can be adapted to technological developments. Those who only sell equipment, on the other hand, might appreciate it when it becomes obsolete and the customer has to buy a new modern machine.
Successful Case Studies as a Starting Point
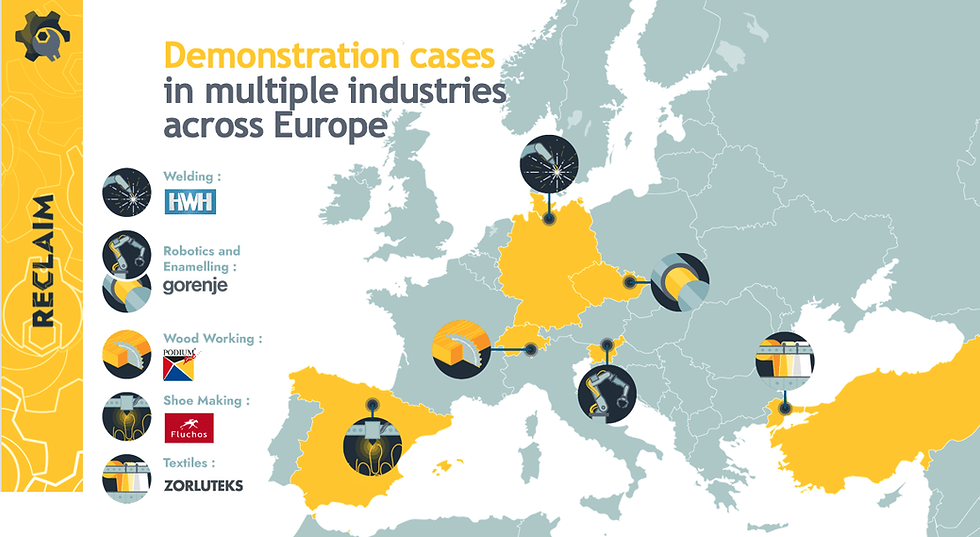
Demo sites. Where and what sectors are refining the approach. Image: RECLAIM/EU.
Friction welding will certainly not be the only business area in which increased attention will be paid in the future to the use of durable machines and the extension of the service life of existing equipment. The EU project alone has already produced four more case studies, from wood processing to shoe manufacturing.
“The variety of possible applications in industry is promising,” said Gralow. The case studies so far, she says, are just the core to start with specific examples.
“That’s when you first notice what challenges you encounter and where the limits of the technology are.”
Thanks to the successfully tackled challenges of the case studies, she remains optimistic: “The approach can definitely be transferred to other sectors in the manufacturing industry.”
You might also like: The Environmental Impact of Broken Technology and the Right to Repair Movement
Kommentare